Landing Gear Suspension System
- Ryan Ng Yu Zhen
- Nov 16, 2016
- 4 min read
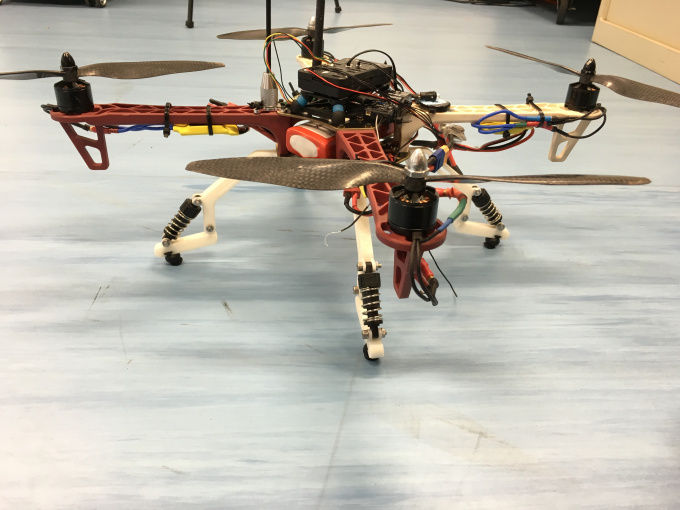
After completing a mini working concept of the tank pulley suspension system, prototype Mk2 did not have the necessary space to fit it in.
Instead of delaying, I began working on the landing gear system for the drone separately, with the intent of it to also be compatible with different drones. The main idea of the landing gears would be:
•To serve as a shock absorber
•To cushion a low to medium height fall
•To protect the electrical hardware within the drone
The initial design of the landing gear was a basic arm with holes that were roughly calculated to save material and 3D printing time, yet still strong enough to support the weight of the drone. The end of the landing gear would just hold a small, commonly used shock absorber.

However, after some research, I found out that the shock absorber used is mainly for negating the smaller, minor vibrations generated by the motors which could affect If our drone were to hit a hard landing impact this shock absorber would not suffice.
Hence, a new design had to be thought up which included suspensions and dampers. The dampers' main function would be to lessen the bouncing effects by the spring.
Design Sketch

Refinements & Dimensioning

3D Printed Model

How does a Suspension work?
A suspension consists of a spring and a damper. The spring's main job is to absorb the shock of the impact and to store the potential energy. Different spring stiffness will result in different characteristics of the suspension. Coil springs are the main type of springs used in my prototype (with others being Leaf Springs or Torsion Bars etc).
Coil Spring Theory relies on the coiled wire acting as a torsion bar, with a load acting upon it at a radius of D/2.
In suspensions, the theoretical linear relationship between load & deflection maybe distorted due to the presence of a damper. As load increases, spring constant is negated as the hydraulic pressure makes it increasingly difficult to compress.
But what exactly are dampers and why are they needed?
Dampers are small pistons with viscous fluids such as oil inside them. As it hits a bump, it will compress the damper and some of the oil will be forced through tiny holes in the piston rod. This increases the pressure of the fluid going through, which will increase the kinetic energy which results in a higher internal energy, ultimately dissipating the force of the bump as heat.
Without dampers, if a vibration is excited it would persist indefinitely. Damping implies a constant resistance proportional to the velocity and a resistance proportional to the square of the velocity. In other words, the faster you are travelling when you hit a bump, the resistance will be the squared of that velocity. Faster speed, more damping resistance.
When a spring is compressed, it stores the energy and the damper helps to dissipate that energy so as to lessen the vibrations felt by the body.
Below are some calculations and rough notes made while working on the suspension system.


Back to the Landing Gears...
Once all refinements and improvements were made, a newer version was 3D printed and test fitted. Then, 3 more legs were produced and mounted to the drone for testing. The shock absorber could be detached at any time and served as an additional accessory.
The drone drop test ranged from as low as 5cm height relative to the ground, and progressively raised higher to as high as waist height. During the first drop test at waist height, the legs broke off from the drone body, and upon inspection I found out that it had been the screws that were unable to withstand the impact force, but the legs and suspension system were fine.
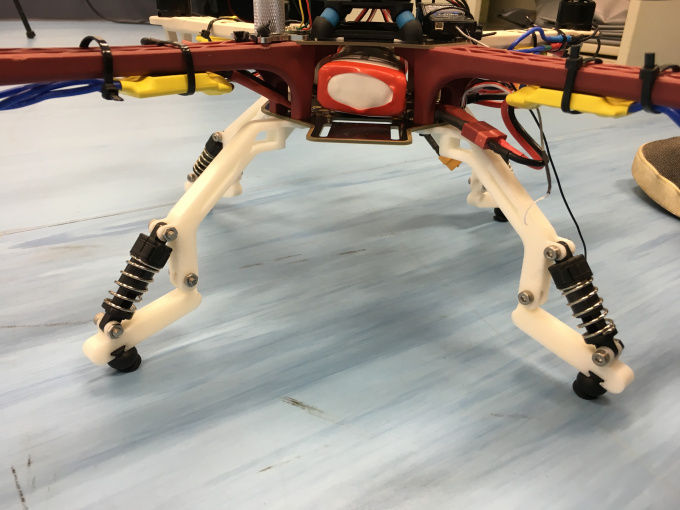
New screws were mounted tightly and this time the drop test was performed again. Due to constraints of this blog site I am unable to upload videos to show the test results. However, the end results were clear. From a height of 5cm to waist height, the drone could withstand the impact force. This would, however, be considered worst case scenario if our drone were to malfunction mid-air or crash land really hard.
Ideally, the drone should be able to land properly each time, but the landing gears main purpose is to cushion the impact in the event of such an incident, and to protect the electrical hardware contained within the drone.
In conclusion & summary, the landing gears should function as a support to hold the drone up when at rest, and to cushion the impact when landing. Should there be a need to switch to a suspension of different length, the bottom arm can easily be detached and interchanged with a longer piece. This makes assembly much easier. The landing gears ultimately act as a sacrificial structure, whereby if the drone were really to crash land at an impact harder than designed for, the landing gears should be the first to break and absorb the impact, but still protect the electrical hardware within. The 3D printed arms can then be re-printed again at little cost, but with the same or better structural integrity.
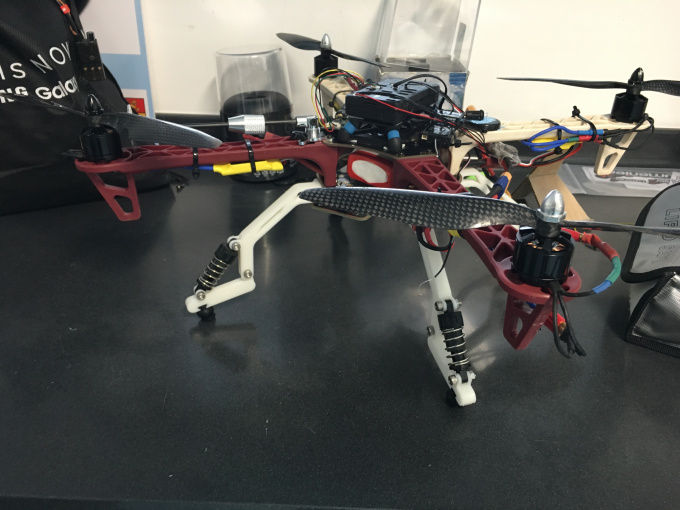
Sincerely,
Ryan Ng
Invictus Mechanical Engineer
Comments