Mark 4 Landing Gears
- Ryan Ng Yu Zhen
- Dec 16, 2016
- 3 min read
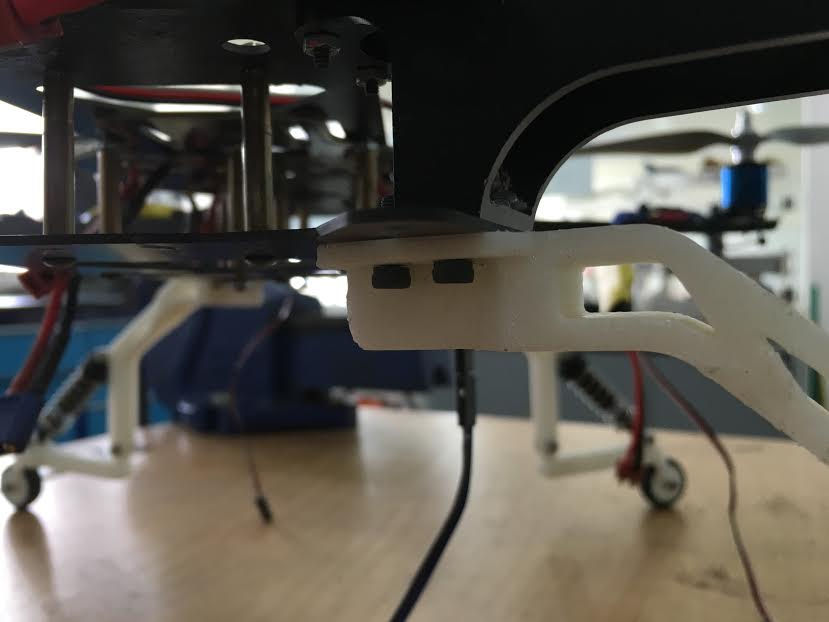
Mark IV retained most of the design as its predecessors, but the top piece was widened to increase strength and durability. By widening the surface structure, the stress acting upon the landing gear would then be reduced. The joint linking to the body (diagram above) was also redesigned to provide a stronger structure, by elongating the rib and changing the shape from a triangle to a rectangle. The reason for this is so that the force is transmitted equally along the rib and there are no weak points, unlike in a triangle, where the start and end edges where they are connected to the body are where the structural stress is acting on the greatest, and where the failure point is most likely to occur. Widening the rib and increasing the length reduces the stress induced as the cross sectional area is now bigger, and is felt evenly along the length.
This design is considered more successful than the rest as during drop-testing, the Mark IV landing gears survived falls from 30cm upwards to 150cm heights with the base weight of 1.5kg to 2kg. This was better than the Mark III & earlier Mark IV designs, which both failed at heights of 40cm & 70cm respectively. The new design surpassed this and was able withstand heights of up to 150cm numerous times carrying 1.5kg to 2kg of weight.
For the final drop test, the new Mark IV landing gears were progressively dropped from 30cm all the way up to 150cm height with a weight of 1.5kg to 2kg. Drops above 100cm were carried out numerous times. The landing gears survived all these falls and did not show any signs of cracks in the joints. From these results I have observed that my new design has successfully eliminated the weak joint of the arm by increasing the length and thickness of the rib, & changing the rib shape from a triangle to a rectangle web, thereby allowing the impact stress to be evenly distributed along the arm. Besides that, the top section of the landing gears were widened to increase the strength as well. The new Mark IV design can be easily re-printed if they fail, but from the tests I can conclude that in the event of a landing failure, the landing gears should not fail if dropped from a height of 150cm or below. This height is acceptable as it covers the minimum landing height, as well as a decent hovering height before landing or take-off.

Interchangeability & Adaptability
The design for the landing gears was done with interchangeability in mind. At the bottom of the pivot arm of Mark II a tiny slot was designed to attach the vibration dampers, as an unsprung mass that could serve as an additional damper to absorb the force. This could be removed at any time should the operator see fit. The vibration damper itself is not necessary but may be attached in the event of a larger vibration or if additional precautions were to be taken. In Mark III & IV this arm has a wheel attachment. The pivot arm length can be redesigned at a longer length to cater for different suspensions or wheel heights, and the angle of the bottom pivot arm relative to the ground can be altered so that the drone’s height of bounce can vary.
Sincerely,
Ryan
Invictus Mechanical Engineer
Comments